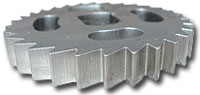
F1で加工したSUS9oの歯車。従来はワイヤ放電加工機で加工していた
志村社長が取り込もうとしたのが、加工の難易度が高く品質管理にも厳しい磁性材料であるケイ素鋼板を使ったモーターコアの試作で、発注元は大手電機メーカー。モーターといっても種類は豊富。しかも必要なトルク、回転数に対応するためにはモーターコアの形状やコアに巻線する回数や巻き方を変えることでいろいろな種類のモーターを製作することができる。用途、種類に応じてモーターの鉄芯用磁性材料であるケイ素鋼板の形状、サイズは千差万別。板厚が0.35mm〜0.5mm程度の薄板のケイ素鋼板を材料にモーターコアを加工するには加工変形やひずみが品質に影響する。熱ひずみの少ないレーザ加工が工法選択のひとつとなっていた。発注元の電機メーカーではレーザ専用マシンを導入してモーターコアの切断加工を行っていたが試作のようなロットが小さな製品では専用マシンでの加工では採算が合わない。そこで目を付けたのがアマダの新鋭機F1。F1は新型NCの高速制御によってピアス時間を大幅に短縮するとともに3軸リニアドライブを採用してトータルの加工時間短縮を実現。また、ビームの揺らぎを最小限に抑えることで高品質の切断面を実現、きめ細かいハイスピードな軸移動によりコーナー部やエッジ部の溶け込みを防止してシャープなエッジ加工、3軸リニアドライブ・フルクローズドループ制御の採用で高精度な位置決め。2つの曲率可変ミラーの採用で切断に最適なビーム径を制御でき、薄板から厚板まで1枚のレンズでカバー、レンズ交換の手間が不要。加工モニタリング、ガウジング、プラズマなどの加工不良の要因となる要素を常時監視して安定加工ができるなどの特長を備えている。パレットチェンジャー(AS-3015F1)で材質、板厚の異なる数種類の材料を棚に管理してスケジュール運転により長時間の連続運転が可能になり、シート材、端材を棚に管理することで材料歩留りを改善できる。他社のレーザマシンでも満足な結果は得られず、アマダの実証加工センターでF1によるサンプル加工をしてもらったら綺麗にできた。...